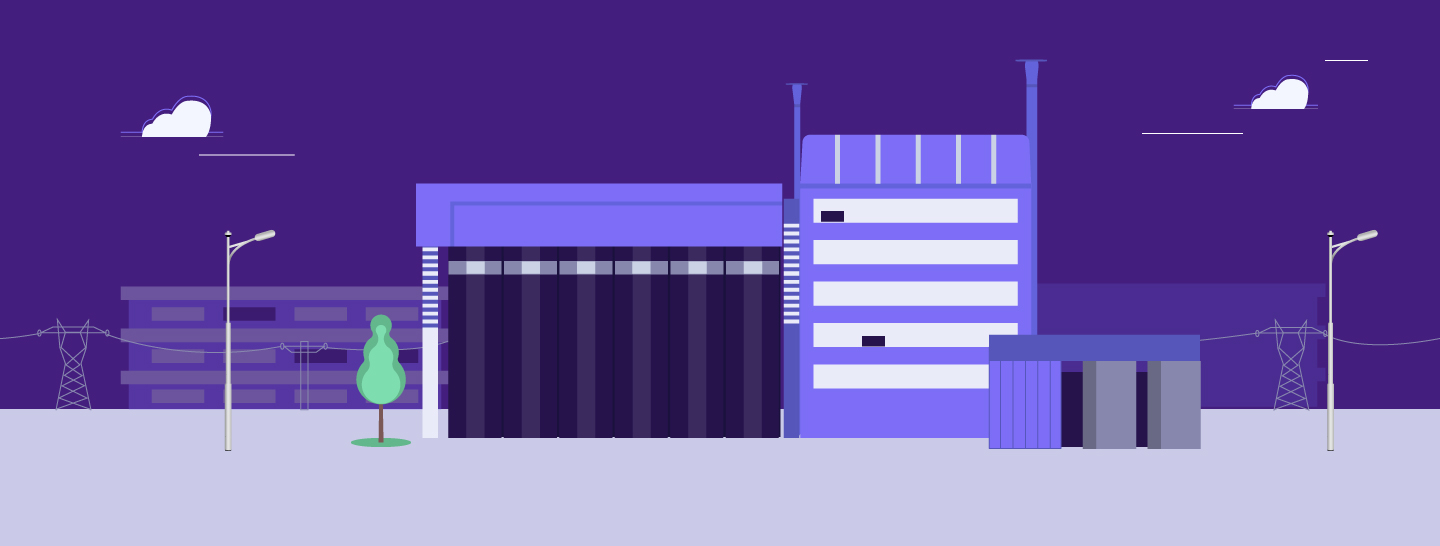
Location
La Coruña, Spain
Client
Showa Denko
Sector
Graphite electrodes producer
Manufacturer Showa Denko asked Endesa X to improve energy efficiency at its graphite electrodes plant by finding a way to reuse the estimated 20%-50% of the energy consumed in the manufacturing process that was being lost in wasted heat. Endesa X designed and executed the installation of a heat recovery system that uses thermal energy produced by the baking ovens, where air exits the chimneys at a temperature of over 1,000ºC, as a heat source. As a result, Showa Denko has reduced initial consumption by 12 GWh of natural gas and 3 GWh of electricity per year.
The client
Japanese multinational Showa Denko is a chemistry company founded in 1939, with 58 subsidiaries in Asia e 41 across Europe, America and Africa. Materials manufactured by Showa Denko are used in everything from yoghurt container packaging to automobiles, flat-screen tvs, PCs and cosmetics. Its Showa Denko Carbon division is the world’s largest supplier of graphite electrodes for use in steel mills. To produce these graphite electrodes, Showa Denko Carbon’s manufacturing process requires baking ovens that operate at extremely high temperatures.
The agreement’s benefits
2,772
tons of CO₂ avoided yearly
16,632
equivalent number of trees
70%
savings on gas boiler consumption
30%
cut in electric heaters consumption
Showa Denko Carbon’s goal was to reduce primary energy consumption, thereby saving on energy costs and improving its carbon footprint.
Endesa X designed and executed the installation of a heat recovery system where waste heat produced by the baking ovens was reused as a source of heat.
Showa Denko Carbon’s plant in northern Spain was able to reduce the consumption of gas boilers by as much as 70%, and by 30% in electricity consumption for the heaters. It cut initial consumption of 12 GWh of natural gas and 3 GWh of electricity each year, since the recovered heat saves the energy that would have been used with the traditional production method.
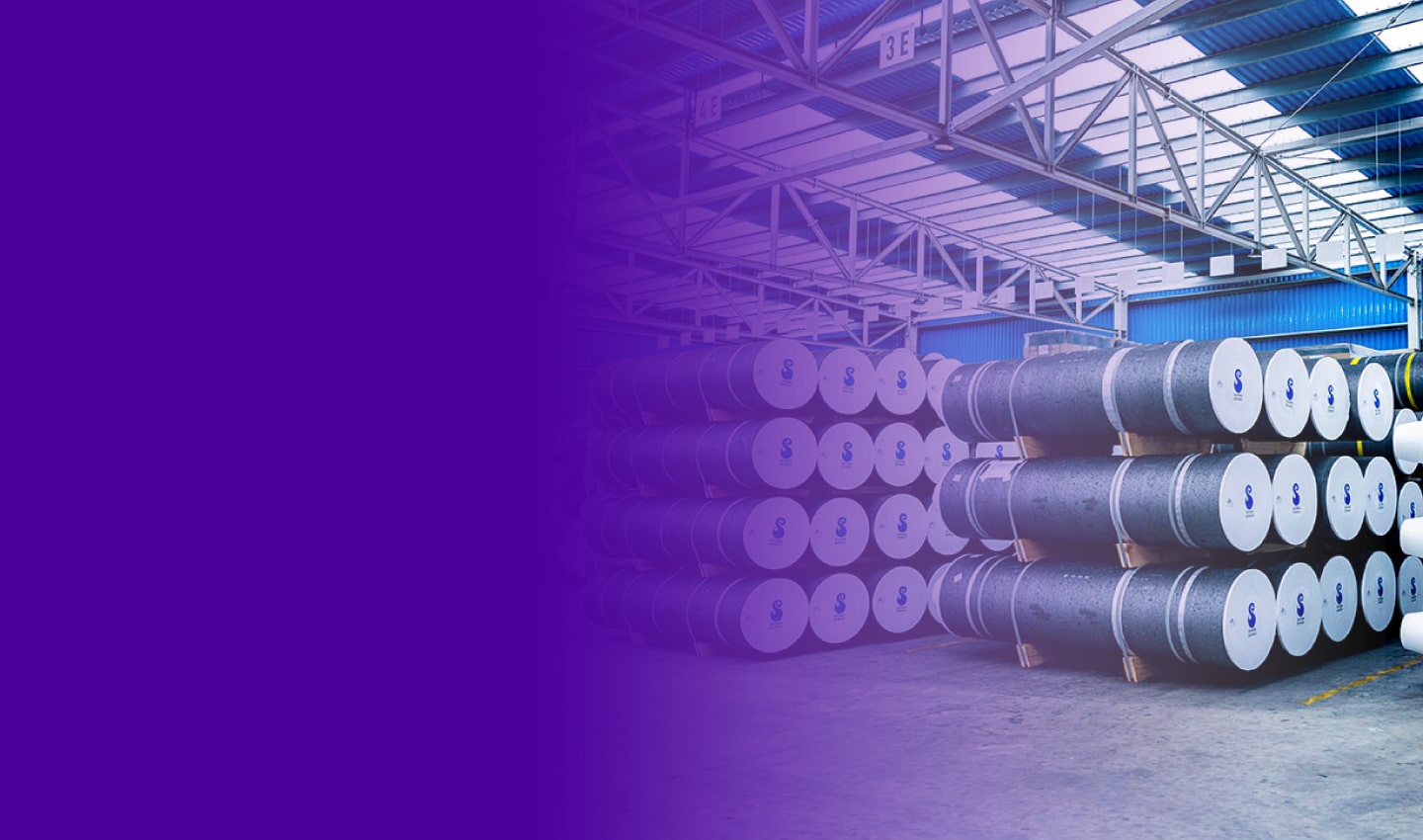
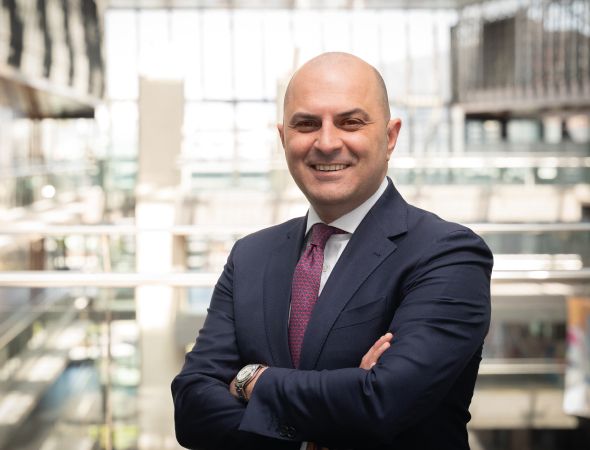
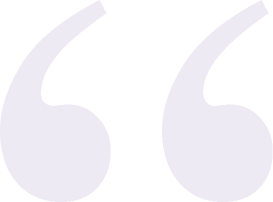
In an intensive manufacturing process like the one at Showa Denko, a circular solution such as heat recovery is the key to reducing energy consumption, dependence on fossil fuels and ensuring the environmental and economic sustainability of the business in the long term. Endesa X has a Net-Zero emissions plan that we adapt to each client, where solutions such as heat recovery are included in a four-phase plan with one goal: To make companies carbon neutral through energy savings and efficiency, the electrification of processes, self-consumption, renewable energy sources and compensation strategies.
Endesa X CEO